Financial Inventory of Production Facilities
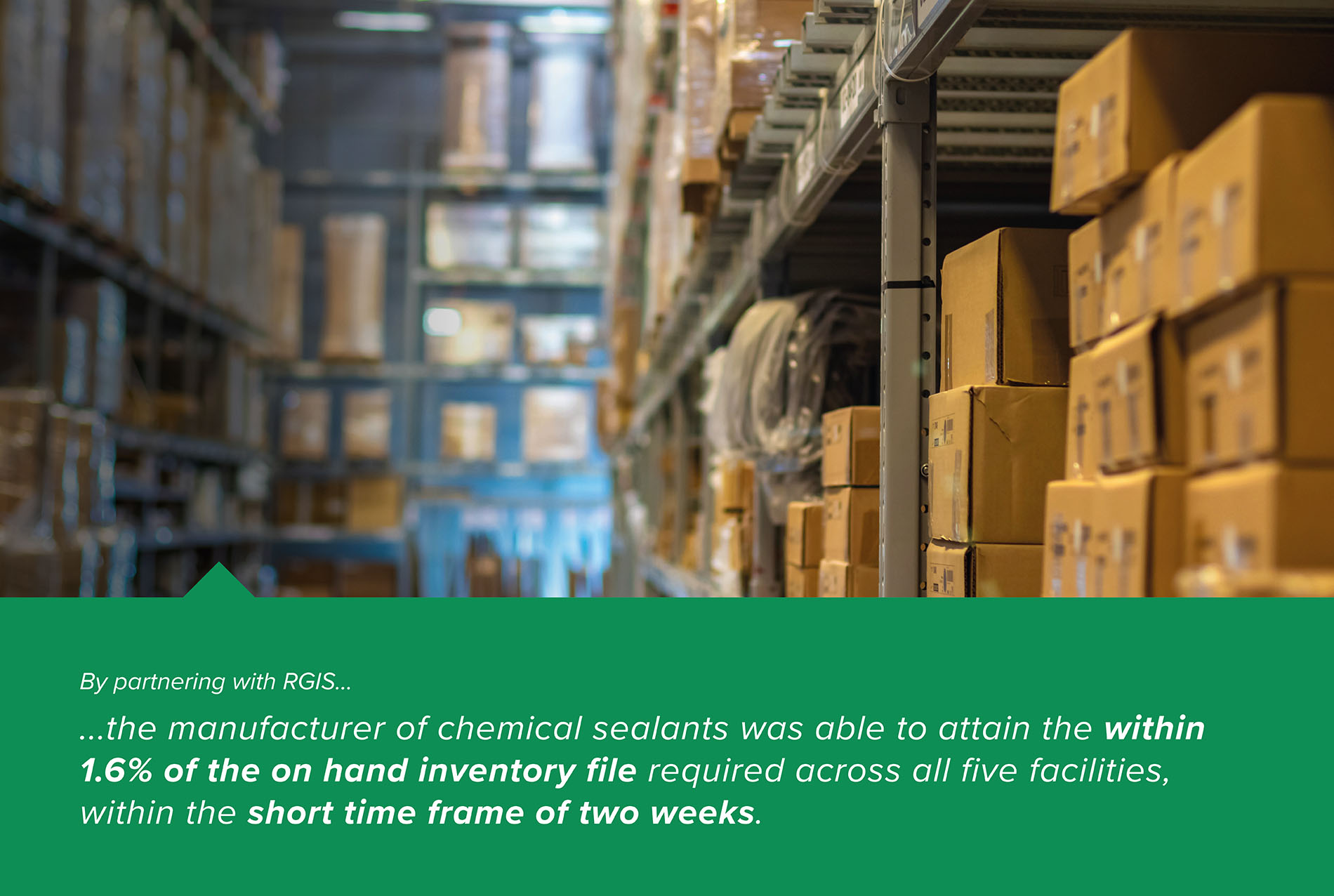
A manufacturer of specialty chemical sealants, founded in 1937, required the support of RGIS. Since these beginnings, they have continued to grow by expanding the offering of chemical and mechanical products to support the tradesman in their work.
REQUIREMENT
The manufacturer of chemical sealants needed a solution of a financial inventory of five facilities in five states on the same day, without having to shut down during the week for production to continue with a purchase of the facilities. The manufacturer required RGIS to provide the following:
- Have national coverage to be able to cover five states
- All five facilities to be counted within a short time frame of two weeks, at the same time
- Variances to be identified
- Each facility to be within 1.6% of the total on hand inventory file
SOLUTION
The manufacturer of chemical sealants partnered with RGIS to complete the financial inventory of production facilities project, and provided the following:
- Scheduled a team of 400 experienced RGIS auditors who worked closely with the in-house team
- Due to the short time frame in order to complete the inventory, RGIS arranged for scissor lift rentals, training and certification for over 70 RGIS team members
- Identified labelling issues that could create additional variances
- Counted both SKU (Stock Keeping Unit) and quantity
- Entered and analysed all the data, to be able to rectify variances
- Ensured no pallets were missed as the pallets were stored double deep
RESULTS
The manufacturer of chemical sealants found by outsourcing the financial inventory of production facilities project to RGIS, the following results were achieved:
- Established processes in the seller’s facilities that the buyers were unfamiliar with:
- Labeling, manufacturing and customer service issues e.g. the customer not getting the correct part
- System issues where the inventory dollars for the product in production was the same as inventory dollars for the raw materials, not accounting for the labour
- A lack of a labeling system and inventory put away processes
- Found that SKU labelling in the production area were not matching
- 10% of the product was not in the system – once the item moved from the floor to production it changed name and was put back on the floor with a different name
- 30% of the product was barcoded differently to the description given
- 15% of the warehouse were mixed SKUs and locations
- Swell in inventory was identified – approximately 1.1% on $20 Million
- Identified inventory that was six years old, that the seller had on the books but the buyer was unaware of